…as sophisticated as a rocket: real-time data and analytics for continuous improvement
…as sophisticated as a rocket: real-time data and analytics for continuous improvement https://bluestarplanning.com/wp-content/themes/corpus/images/empty/thumbnail.jpg 150 150 Jorrit Reedijk https://secure.gravatar.com/avatar/63b95b43daf18a4f0aaacc6fdf2bf8d381d8ea25d6e4f6f12a67eca2ac906378?s=96&d=mm&r=g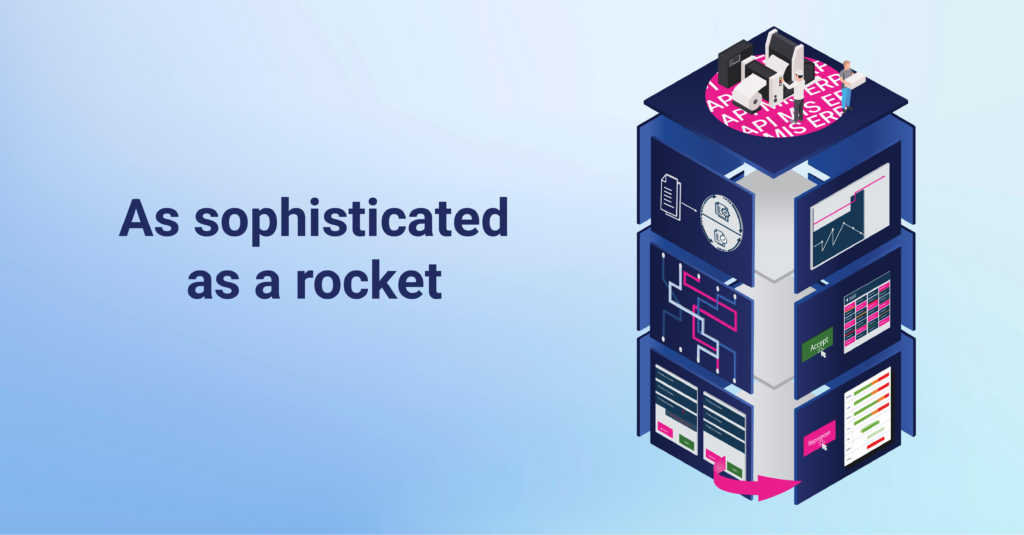
In our previous blogpost we discussed the implementation process of our planning and scheduling platform and how we use technology to keep an extremely small implementation footprint. This time, we’ll go into our third and fourth implementation steps will and what they bring to your production, as well as the benefits of full implementation of our platform.
The 3rd implementation step: Constraint kit, compute with constraints
This pillar of optimization includes planning and scheduling assistance for strict constraints and less strict constraints, integrated into the automated sequencing and sophisticated calculation implementation of your production process, the components of earlier implementation steps in pillars 2 & 3. The constraints span the availability of tools and raw materials you need for production, as well as delivery deadlines. All these restrictions are incorporated into our platform, providing you with a more accurate estimate of your production process and enabling our algorithms to generate better planning proposals.
The 4th implementation step: Real-time registration and deep monitoring
The fourth step in the implementation cycle is where preparation and real-time monitoring come together for continuous improvement. By monitoring production progress in real-time the short-time estimation accuracy becomes even higher and the long-time predictions more accurate.
With a combination of integrating your existing systems and machines, and retrofitting hardware in your production environment, real-time registrations and dataflows are built. Not only are you kept minutely up to date on the current status of deliverables, but you also prepare for big data usage and apply pattern matching (or Artificial Intelligence as some would call it) for even better forecasting in the future.
In each of the four pillars of optimization, the steps for implementation, the Blue Star Planning platform is tailored to your specific production environment and requirements. The secure platform is available from every location and device, so information can be shared throughout the factory for each specific user role.
And to ensure that we live up to the level of commitment we make to you, our team of consultants and support engineers are available for support and additional consultations to let your planner get to most out of our software.
If you want to learn more about planning proposals and our production platform for planning and scheduling, let us know at hello@bluestarplanning.com and we will get back to you as soon as possible to schedule a demo.