As easy as 1-2-3: simple steps for onboarding
As easy as 1-2-3: simple steps for onboarding https://bluestarplanning.com/wp-content/themes/corpus/images/empty/thumbnail.jpg 150 150 Ivan https://secure.gravatar.com/avatar/2f24009c98439aad11227413f689a69a8a3b43fcbbed67570bab15fb53fa3f0f?s=96&d=mm&r=g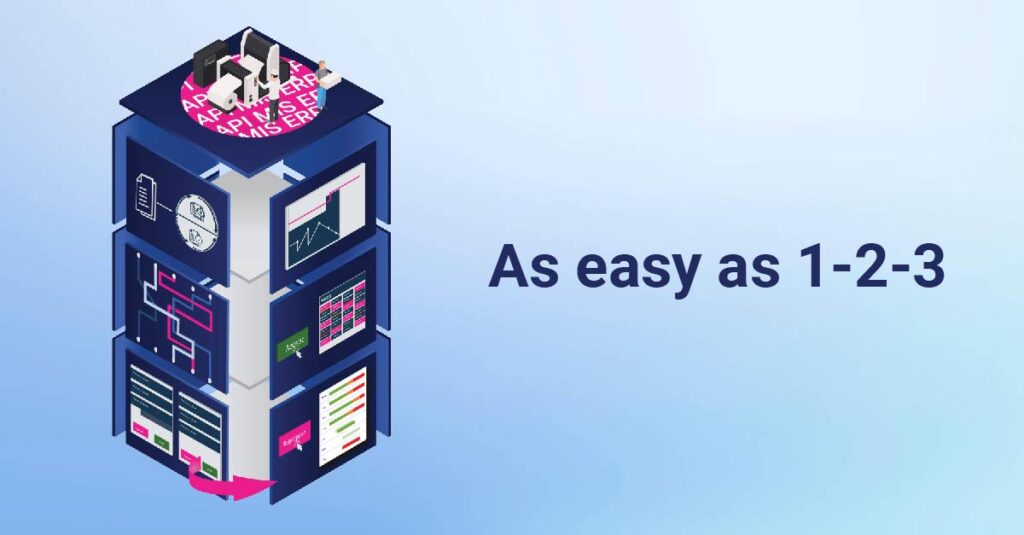
Implementing a new software platform should always be a process that can be divided into smaller steps and implementing Blue Star Planning’s custom-tailored and secure platform is certainly no different and has a really low implementation footprint. The steps to implement complete production automation (these steps we call pillars of optimization) are divided in such a way that each implementation step optimizes a certain part of your production planning. For example, at the start of the first step, our 1st pillar will offer out-of-the-box improvement of 15% of your production planning compared to existing systems. For further optimization of your production runs, the 2nd pillar is setting up optimal calculations. Track raw material and tooling and applying constraint-based planning comes with the 3rd pillar. Full optimization with live tracking, sensory data, and autonomous planning is how you eventually automate your factory, the way to go and top-most achievable, the 4th pillar of optimization and the last step in the process.
What is specific about the implementation process, is that our steps for optimization do not necessarily lean on each other. You can implement one and not the other. We’ll always work together to choose which options to implement, to seamlessly work together with your existing software, and improves your production process where needed first.
The 1st implementation step: Integrated automatic sequencing
If you’re looking to get started with specialized metrics and production analysis, the 1st implementation option is a great starting point. With your existing production data as input, it solves the problem of quickly determining a production sequence and offers a real-time view of your production through our Planboard. At the same time the Planboard offers an interactive comparison of your production planning. Our specialized algorithms work in the background and determines an optimal production sequence for each workstation, creates a planning proposal based and lets you work out different what-if scenarios. Each one of these proposals are created as intelligent assistance to your production manager who is still the main decision maker in your factory. Basically, he will get the ideal production plan according to regular and special orders scheduled in the factory.
This implementation process is easy and fast to implement and offers on average a 30% increase in productivity compared to systems that say to have comparable functionality, which makes it one of our most sought-after products for small and medium sized companies.
The 2nd implementation step: Optimal layout for higher productivity
The 2nd implementation option is everything that our 1st option and integrates additional data inputs for a more sophisticated calculation. In addition to almost instantly creating planning proposals, this implementation solution takes in the changeover times and production time into account, as well as transport times and material consumption. This allows your production manager to handle a larger number of production machines and a bigger production floor area without a hassle, as our production planning algorithm is there to calculate the ideal production statrt time for every single machine on your production floor.
This implementation option is great for companies that are not ready to fully automate production processes but want to experience the advantages of automated production planning and scheduling systems that larger factories use. The best thing might be that you can have it for a fraction of price and time to implement which is achieved through integration with your existing resource planning system instead of migrating to a newer and more expensive one.
If you’re looking to automate more than production planning, our 3rd and 4th implementation options work within deep monitoring and constraints calculations to automate more different processes in your factory production. Read more about them in our next blog post.